Metoda 5S: Zasady, wdrożenie i korzyści
Standard 5S to system zarządzania, który pomaga organizacjom usprawnić swoje procesy, zwiększyć wydajność i poprawić jakość pracy. W tym artykule omówimy historię metody 5S, jej związek z lean management, podstawowe elementy, zasady, wdrożenie oraz korzyści płynące z jej stosowania. Zapoznasz się również z informacjami na temat audytu 5S i utrzymania praktyk związanych z tą metodą.
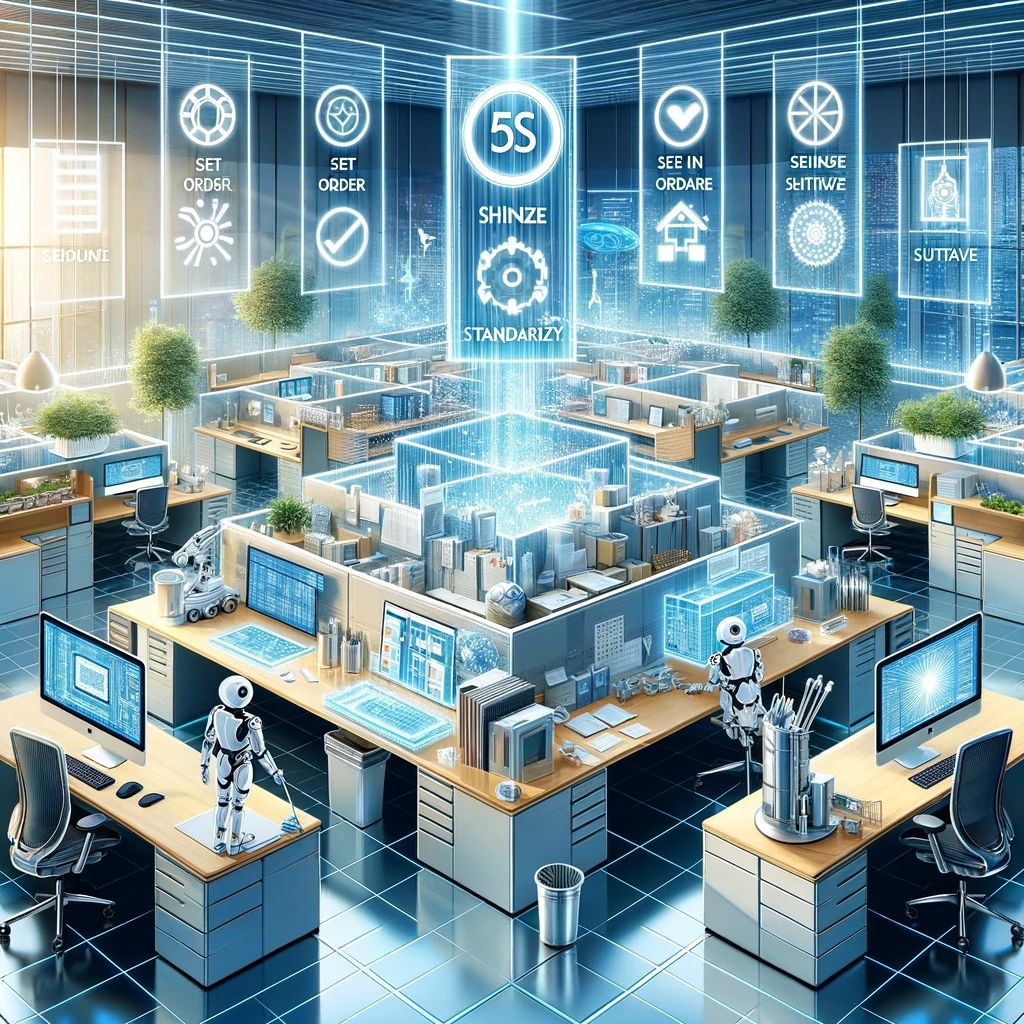
Spis treści
Co to jest metoda 5S?
Metoda 5S to system zarządzania, który ma na celu usprawnienie procesów produkcyjnych, zwiększenie wydajności pracy oraz poprawę organizacji miejsca pracy. Składa się z pięciu kluczowych elementów, które są oparte na japońskich słowach: seiri, seiton, seiso, seiketsu i shitsuke. Standard 5S jest często stosowany w ramach koncepcji lean management, która dąży do eliminacji marnotrawstwa i ciągłego doskonalenia procesów.
Historia metody 5S i jej związek z lean management
Historia metody 5S sięga lat 60. XX wieku, kiedy to japońskie przedsiębiorstwa zaczęły wprowadzać nowe techniki zarządzania jakością w celu zwiększenia konkurencyjności na rynku. Metoda 5S została opracowana przez Takashi Osady, który zainspirował się amerykańskim systemem zarządzania jakością Total Quality Management (TQM). Wraz z ewolucją metody 5S, jej zasady zostały włączone do koncepcji lean management, która wywodzi się z systemu produkcyjnego Toyoty. Lean management dąży do eliminacji wszelkiego rodzaju marnotrawstwa, a metoda 5S stanowi jeden z kluczowych elementów tego podejścia.
Podstawowe elementy metody 5S
5S to pięć zasad, które mają na celu usprawnienie organizacji miejsca pracy i procesów produkcyjnych. Są to:
- Seiri (sortowanie) – eliminacja zbędnych przedmiotów i materiałów z miejsca pracy.
- Seiton (systematyka) – uporządkowanie narzędzi i materiałów w sposób umożliwiający łatwy dostęp i efektywne wykorzystanie.
- Seiso (sprzątanie) – utrzymanie czystości i porządku na stanowiskach pracy.
- Seiketsu (standaryzacja) – opracowanie i wdrożenie standardów pracy, które mają na celu utrzymanie porządku i efektywności procesów.
- Shitsuke (samodyscyplina) – kształtowanie postaw pracowników, które sprzyjają przestrzeganiu zasad 5S i ciągłemu doskonaleniu.
Jak działa metoda 5S?
Działanie metody 5S polega na systematycznym wdrażaniu pięciu zasad w organizacji, zaczynając od sortowania zbędnych przedmiotów, poprzez uporządkowanie narzędzi i materiałów, aż po utrzymanie czystości i porządku na stanowiskach pracy. Następnie, w ramach standaryzacji, opracowywane są procedury i instrukcje, które mają na celu utrzymanie osiągniętego poziomu organizacji. Ostatnim etapem jest kształtowanie postaw pracowników, które sprzyjają przestrzeganiu zasad 5S i ciągłemu doskonaleniu. Wdrożenie metody 5S wymaga zaangażowania zarówno kierownictwa, jak i pracowników, a jej efektywność zależy od systematyczności i konsekwencji w realizacji poszczególnych etapów.
Zasady 5S lean management
Zasady 5S w obszarze lean management to kluczowe elementy metody 5S, które mają na celu usprawnienie procesów produkcyjnych, zwiększenie wydajności pracy oraz poprawę organizacji miejsca pracy. W ramach lean management, zasady 5S są stosowane w celu eliminacji marnotrawstwa i ciągłego doskonalenia procesów.
Sortowanie, systematyka, sprzątanie, standaryzacja, samodyscyplina: Zrozumienie zasad 5S
Sortowanie (seiri) polega na eliminacji zbędnych przedmiotów i materiałów z miejsca pracy, co pozwala na skupienie się na tym, co naprawdę jest potrzebne do realizacji zadań. Systematyka (seiton) to uporządkowanie narzędzi i materiałów w sposób umożliwiający łatwy dostęp i efektywne wykorzystanie. Sprzątanie (seiso) to utrzymanie czystości i porządku na stanowiskach pracy, co przyczynia się do lepszego funkcjonowania pracowników i sprzętu. Standaryzacja (seiketsu) to opracowanie i wdrożenie standardów pracy, które mają na celu utrzymanie porządku i efektywności procesów. Ostatnia zasada, samodyscyplina (shitsuke), dotyczy kształtowania postaw pracowników, które sprzyjają przestrzeganiu zasad 5S i ciągłemu doskonaleniu.
Zasady 5S na produkcji: Praktyczne zastosowanie
Zasady 5S na produkcji można zastosować na różnych etapach procesu produkcyjnego. Przykłady zastosowania zasad 5S w środowisku produkcyjnym obejmują:
- Sortowanie i oznaczanie narzędzi oraz materiałów, co ułatwia ich szybkie odnalezienie i zmniejsza czas przestoju.
- Systematyczne utrzymanie czystości maszyn i urządzeń, co przyczynia się do wydłużenia ich żywotności i zmniejszenia awarii.
- Standaryzacja procedur pracy, co pozwala na łatwiejsze szkolenie nowych pracowników i eliminację błędów wynikających z niejednoznacznych instrukcji.
- Wprowadzenie samodyscypliny wśród pracowników, co przyczynia się do utrzymania porządku i ciągłego doskonalenia procesów produkcyjnych.
Metoda 6S: Rozszerzenie metody 5S
Metoda 6S to rozszerzenie metody 5S, które wprowadza dodatkowy element – bezpieczeństwo (safety). W ramach metody 6S, oprócz pięciu zasad 5S, uwzględnia się również aspekty związane z bezpieczeństwem pracy, takie jak:
- Eliminacja zagrożeń w miejscu pracy, np. poprzez zabezpieczenie maszyn czy uporządkowanie przewodów elektrycznych.
- Wprowadzenie procedur awaryjnych i szkolenie pracowników z zakresu pierwszej pomocy.
- Regularne przeglądy i kontrole stanowisk pracy pod kątem bezpieczeństwa.
Wprowadzenie metody 6S pozwala na jeszcze bardziej kompleksowe podejście do zarządzania jakością i organizacji miejsca pracy, uwzględniając również aspekty związane z bezpieczeństwem pracowników.
Wdrożenie w przedsiębiorstwie standardu 6S, stanowi dobrą bazę do wdrożenia w organizacji standardu ISO 45001:2018 System Zarządzania Bezpieczeństwem i Higieną Pracy.
Wdrażanie metody 5S w praktyce
Wdrażanie standardu 5S to proces, który obejmuje kilka etapów, od planowania po realizację. Wdrożenie metody 5S w przedsiębiorstwie może przynieść wiele korzyści, takich jak zwiększenie wydajności pracy, eliminacja marnotrawstwa czy poprawa organizacji miejsca pracy.
Jak przygotować się do wdrożenia metody 5S?
Aby przygotować się do wdrożenia metody 5S, warto zastosować kilka wskazówek:
- Przeprowadź analizę stanu obecnego miejsca pracy, aby zidentyfikować obszary wymagające poprawy.
- Ustal cele i priorytety wdrożenia metody 5S, takie jak redukcja przestojów czy zwiększenie wydajności.
- Przygotuj plan wdrożenia, który uwzględnia kolejne etapy wdrażania metody 5S oraz harmonogram działań.
- Zaangażuj pracowników w proces wdrożenia, przeprowadzając szkolenia i warsztaty dotyczące zasad 5S.
- Monitoruj postępy wdrażania metody 5S i wprowadzaj korekty w razie potrzeby.
Przykłady zastosowania metody 5S w przedsiębiorstwach
Przykłady zastosowania metody 5S można znaleźć w różnych typach przedsiębiorstw, niezależnie od branży czy wielkości firmy. Oto kilka przykładów:
- W magazynach: uporządkowanie przestrzeni magazynowej, oznaczenie miejsc składowania towarów, utrzymanie czystości i porządku.
- W biurach: organizacja stanowisk pracy, eliminacja zbędnych dokumentów, wprowadzenie systemu zarządzania dokumentacją.
- W warsztatach samochodowych: sortowanie i oznaczanie narzędzi, utrzymanie czystości i porządku, standaryzacja procedur pracy.
- W przedsiębiorstwach produkcyjnych: optymalizacja procesów produkcyjnych, eliminacja marnotrawstwa, standaryzacja procedur pracy.
Problemy, które mogą napotkać podczas wdrażania metody 5S
Podczas wdrażania metody 5S mogą wystąpić różne wyzwania i problemy, takie jak:
- Opór ze strony pracowników, wynikający z obaw przed zmianami czy braku zrozumienia celów wdrożenia metody 5S.
- Trudności z utrzymaniem zaangażowania pracowników w dłuższej perspektywie, co może prowadzić do powrotu do starych nawyków.
- Brak odpowiednich zasobów, takich jak czas czy środki finansowe, na wdrożenie metody 5S.
- Problemy z monitorowaniem postępów wdrażania metody 5S i wprowadzaniem korekt w razie potrzeby.
Aby uniknąć tych problemów, warto zadbać o właściwe przygotowanie do wdrożenia metody 5S, zaangażowanie pracowników oraz regularne monitorowanie postępów i wprowadzanie korekt w razie potrzeby. Można również rozważyć wparcie wdrożenia standardu 5S, przez firmę zewnętrzną.
Korzyści z wdrożenia metody 5S
Wdrożenie metody 5S w przedsiębiorstwie przynosi wiele korzyści, które wpływają na poprawę funkcjonowania firmy. Wśród nich można wymienić zwiększenie wydajności pracy, eliminację marnotrawstwa, lepszą organizację miejsca pracy oraz wizualizację i dostosowanie stanowiska pracy zgodnie z zasadami 5S.
Zwiększenie wydajności pracy dzięki metodzie 5S
Wprowadzenie 5S w firmie przyczynia się do zwiększenia wydajności pracy poprzez uporządkowanie i standaryzację procesów oraz eliminację zbędnych czynności. Dzięki temu pracownicy mogą skupić się na wykonywaniu swoich zadań, co przekłada się na lepsze wyniki pracy. Ponadto, metoda 5S ułatwia identyfikację problemów i szybkie reagowanie na nie, co pozwala na unikanie przestojów i strat czasu.
Eliminacja marnotrawstwa i lepsza organizacja miejsca pracy
Metoda 5S pomaga w eliminacji marnotrawstwa oraz poprawie organizacji miejsca pracy. Dzięki zastosowaniu zasad sortowania, systematyki i sprzątania, przedsiębiorstwa mogą pozbyć się zbędnych przedmiotów, co przekłada się na większą przestrzeń roboczą i lepsze warunki pracy. Ponadto, uporządkowanie miejsca pracy ułatwia dostęp do potrzebnych narzędzi i materiałów, co przyspiesza realizację zadań.
Wizualizacja i dostosowanie stanowiska pracy zgodnie z zasadami 5S
Zasady 5S mogą być zastosowane do wizualizacji stanowiska pracy oraz dostosowania stanowiska pracy do potrzeb pracowników. Wizualizacja polega na oznaczaniu miejsc przechowywania narzędzi, materiałów czy dokumentów, co ułatwia ich odnalezienie i utrzymanie porządku. Dostosowanie stanowiska pracy zgodnie z zasadami 5S może obejmować takie działania, jak regulacja wysokości biurka czy krzesła, optymalne rozmieszczenie sprzętu czy wprowadzenie ergonomicznych rozwiązań. Dzięki temu pracownicy mogą wykonywać swoje zadania w komfortowych warunkach, co przekłada się na lepszą jakość pracy.
Podsumowując, korzyści z wdrożenia metody 5S są niezaprzeczalne i wpływają na poprawę funkcjonowania przedsiębiorstwa na wielu płaszczyznach. Warto zatem rozważyć wdrożenie tej metody w swojej firmie, aby czerpać z niej korzyści w dłuższej perspektywie.
Audyt 5S i utrzymanie praktyk 5S
W celu utrzymania praktyk 5S na wysokim poziomie, niezbędne jest przeprowadzenie regularnych audytów 5S. Audyt pozwala na ocenę efektywności wdrożonych działań oraz identyfikację obszarów wymagających poprawy. W tej części artykułu omówimy, jak przeprowadzić audyt 5S oraz jak utrzymać stanowisko pracy zgodnie z zasadami 5S, aby zapewnić dobrą organizację miejsca pracy.
Jak przeprowadzić audyt 5S?
Przeprowadzenie audytu 5S wymaga przestrzegania kilku kroków, które pomogą w ocenie stanu wdrożenia metody 5S w przedsiębiorstwie. Oto kilka wskazówek, które warto wziąć pod uwagę podczas audytu:
- Przygotuj listę kontrolną, która obejmuje wszystkie aspekty zasad 5S. Lista kontrolna powinna być dostosowana do specyfiki firmy i branży.
- Wybierz zespół audytowy, który będzie odpowiedzialny za przeprowadzenie audytu. Zespół powinien być złożony z osób znających metodykę 5S oraz mających doświadczenie w przeprowadzaniu audytów.
- Przeprowadź audyt na podstawie listy kontrolnej, oceniając każdy z punktów. Zwróć uwagę na wszelkie nieprawidłowości oraz obszary wymagające poprawy.
- Dokumentuj wyniki audytu, wskazując na osiągnięcia oraz obszary do poprawy. Wyniki audytu powinny być przedstawione zarówno w formie pisemnej, jak i graficznej (np. za pomocą wykresów).
- Przedstaw wyniki audytu zespołowi oraz kierownictwu firmy. Omów wnioski oraz zaproponuj działania naprawcze w celu poprawy efektywności wdrożenia metody 5S.
Utrzymanie stanowiska pracy zgodnie z zasadami 5S
Utrzymanie stanowiska pracy zgodnie z zasadami 5S jest kluczowe dla utrzymania wysokiej efektywności oraz dobrej organizacji miejsca pracy. Oto kilka praktyk, które pomogą w utrzymaniu porządku i efektywności na stanowisku pracy:
- Regularne sprzątanie i utrzymanie czystości na stanowisku pracy.
- Uporządkowanie narzędzi oraz materiałów, tak aby były łatwo dostępne i widoczne.
- Stosowanie oznaczeń wizualnych, takich jak etykiety czy kolorowe taśmy, w celu ułatwienia identyfikacji miejsca przechowywania narzędzi i materiałów.
- Wprowadzenie rutynowych kontroli oraz audytów 5S, aby monitorować efektywność wdrożenia metody oraz identyfikować obszary wymagające poprawy.
Dobra organizacja miejsca pracy jako klucz do utrzymania metody 5S
Dobra organizacja miejsca pracy jest kluczowa dla utrzymania standardu 5S, ponieważ pozwala na efektywne wykorzystanie przestrzeni oraz zasobów. Oto kilka aspektów, na które warto zwrócić uwagę, aby zapewnić dobrą organizację miejsca pracy:
- Minimalizacja zbędnych przedmiotów oraz materiałów, które mogą utrudniać pracę i wpływać na efektywność.
- Stosowanie ergonomicznych rozwiązań, takich jak regulowane krzesła czy biurka, które pozwalają na dostosowanie stanowiska pracy do potrzeb pracownika.
- Wprowadzenie systemów przechowywania, które ułatwiają utrzymanie porządku oraz dostęp do potrzebnych narzędzi i materiałów.
- Stosowanie oznaczeń wizualnych oraz instrukcji, które pomagają w utrzymaniu porządku oraz efektywności pracy.
Podsumowując, przeprowadzenie audytu 5S oraz utrzymanie praktyk 5S są kluczowe dla utrzymania wysokiej efektywności oraz dobrej organizacji miejsca pracy. Regularne audyty oraz stosowanie zasad 5S na co dzień pozwala na ciągłe doskonalenie procesów oraz utrzymanie wysokiej jakości pracy.
Podsumowanie
Przedstawiliśmy kompleksowy przewodnik po standardzie 5S, omawiając jej zasady, wdrożenie oraz korzyści płynące z jej stosowania. Metoda 5S, wywodząca się z lean management, składa się z pięciu zasad: sortowanie, systematyka, sprzątanie, standaryzacja oraz samodyscyplina. W praktyce, metoda 5S pozwala na zwiększenie wydajności pracy, eliminację marnotrawstwa oraz lepszą organizację miejsca pracy.
Wdrożenie metody 5S w przedsiębiorstwie wymaga odpowiedniego przygotowania, w tym analizy obecnego stanu oraz opracowania planu działań. Przykłady zastosowania metody 5S obejmują różne branże, od produkcji po usługi. Warto również zwrócić uwagę na możliwe problemy, które mogą napotkać podczas wdrażania metody 5S, takie jak opór ze strony pracowników czy brak wsparcia ze strony kierownictwa.
Korzyści z wdrożenia metody 5S obejmują zwiększenie wydajności pracy, eliminację marnotrawstwa oraz lepszą organizację miejsca pracy. Wizualizacja i dostosowanie stanowiska pracy zgodnie z zasadami 5S są kluczowe dla osiągnięcia tych korzyści. Audyt 5S oraz utrzymanie praktyk 5S są niezbędne dla utrzymania wysokiej efektywności oraz dobrej organizacji miejsca pracy.
Podsumowując, metoda 5S jest skutecznym narzędziem zarządzania, które pozwala na ciągłe doskonalenie procesów oraz utrzymanie wysokiej jakości pracy. Stosowanie zasad 5S na co dzień oraz przeprowadzanie regularnych audytów 5S są kluczowe dla utrzymania wysokiej efektywności oraz dobrej organizacji miejsca pracy.
FAQ
Metoda 5S to system zarządzania, który koncentruje się na organizacji miejsca pracy, aby zwiększyć efektywność, bezpieczeństwo i jakość. Składa się z pięciu zasad: sortowanie (seiri), systematyka (seiton), sprzątanie (seiso), standaryzacja (seiketsu) i samodyscyplina (shitsuke). Te zasady pomagają usprawnić procesy produkcyjne i operacyjne poprzez eliminację zbędnych przedmiotów, uporządkowanie narzędzi i materiałów, utrzymanie czystości, standaryzację procedur i promowanie samodyscypliny wśród pracowników.
Metoda 5S powstała w Japonii w latach 60. XX wieku, a jej zasady były rozwijane w ramach japońskiego systemu zarządzania jakością. Metodę opracował Takashi Osada, który zainspirował się amerykańskim Total Quality Management (TQM). Wkrótce stała się ona integralną częścią Toyota Production System (TPS), który jest fundamentem lean management, koncepcji skupiającej się na eliminacji marnotrawstwa i ciągłym doskonaleniu procesów
Podstawowe elementy metody 5S to:
Seiri (sortowanie): Usunięcie z miejsca pracy wszystkiego, co jest zbędne.
Seiton (systematyka): Uporządkowanie niezbędnych przedmiotów tak, aby były łatwo dostępne.
Seiso (sprzątanie): Regularne czyszczenie miejsca pracy, aby utrzymać porządek.
Seiketsu (standaryzacja): Opracowanie i wdrożenie standardów pracy, które utrzymują porządek i efektywność.
Shitsuke (samodyscyplina): Kształtowanie i utrzymanie dyscypliny w przestrzeganiu zasad 5S.
Metoda 5S działa poprzez systematyczne wdrażanie i utrzymywanie pięciu zasad w miejscu pracy:
Rozpoczyna się od sortowania zbędnych przedmiotów.
Następnie przechodzi się do systematyki, czyli uporządkowania potrzebnych narzędzi i materiałów.
Kolejny krok to sprzątanie, aby utrzymać czystość i porządek.
Standaryzacja obejmuje tworzenie procedur i standardów utrzymania porządku.
Ostatni etap to samodyscyplina, która polega na promowaniu ciągłego przestrzegania zasad 5S.
W ramach lean management, zasady 5S są kluczowe dla eliminacji marnotrawstwa i ciągłego doskonalenia:
Sortowanie: Skupienie się na potrzebnych zasobach i eliminacja zbędnych elementów.
Systematyka: Organizowanie przestrzeni roboczej w sposób, który ułatwia dostęp do potrzebnych narzędzi.
Sprzątanie: Regularne utrzymanie czystości, aby zapobiec problemom operacyjnym.
Standaryzacja: Tworzenie standardowych procedur dla zachowania porządku.
Samodyscyplina: Promowanie ciągłego przestrzegania zasad i doskonalenia.
Zasady 5S można zastosować w różnych kontekstach produkcyjnych:
Sortowanie narzędzi i materiałów, aby tylko potrzebne rzeczy były dostępne.
Systematyka w rozmieszczeniu narzędzi, co skraca czas przestoju.
Sprzątanie maszyn i stanowisk pracy, co zwiększa ich wydajność i zmniejsza awaryjność.
Standaryzacja procedur pracy, co ułatwia szkolenie nowych pracowników.
Samodyscyplina w utrzymaniu porządku, co wspiera ciągłe doskonalenie procesów.
Metoda 6S to rozszerzenie metody 5S o dodatkowy element – Safety (bezpieczeństwo). Uwzględnia aspekty związane z bezpieczeństwem pracy, takie jak:
Eliminacja zagrożeń: Usuwanie lub zabezpieczanie potencjalnych zagrożeń.
Procedury awaryjne: Tworzenie i wdrażanie procedur w sytuacjach awaryjnych.
Regularne przeglądy: Prowadzenie regularnych kontroli bezpieczeństwa stanowisk pracy.
Wdrożenie metody 5S wymaga kilku kluczowych kroków:
Przygotowanie: Analiza obecnego stanu miejsca pracy i określenie obszarów do poprawy.
Planowanie: Ustalenie celów wdrożenia i opracowanie planu działań.
Szkolenie: Przeprowadzenie szkoleń i warsztatów dla pracowników.
Realizacja: Wdrożenie zasad 5S zgodnie z planem.
Monitorowanie: Regularne sprawdzanie postępów i wprowadzanie korekt.
Metoda 5S jest uniwersalna i może być stosowana w różnych branżach:
Magazyny: Oznaczanie miejsc składowania i eliminacja zbędnych zapasów.
Biura: Organizacja przestrzeni roboczej i systematyzacja dokumentów.
Warsztaty samochodowe: Uporządkowanie narzędzi i przestrzeni roboczej.
Przedsiębiorstwa produkcyjne: Optymalizacja procesów i redukcja marnotrawstwa.
Podczas wdrażania metody 5S mogą wystąpić różne wyzwania:
Opór ze strony pracowników: Strach przed zmianami lub brak zrozumienia dla celów 5S.
Utrzymanie zaangażowania: Trudności z utrzymaniem ciągłej motywacji pracowników.
Brak zasobów: Ograniczone zasoby czasowe lub finansowe.
Monitorowanie postępów: Trudności w regularnym sprawdzaniu i ocenie postępów wdrożenia.
Korzyści z wdrożenia metody 5S obejmują:
Zwiększenie wydajności pracy: Poprawa organizacji miejsca pracy i eliminacja zbędnych czynności.
Eliminacja marnotrawstwa: Usunięcie niepotrzebnych przedmiotów i usprawnienie procesów.
Lepsza organizacja miejsca pracy: Łatwiejszy dostęp do narzędzi i materiałów.
Wizualizacja i dostosowanie stanowiska pracy: Ułatwienie pracy poprzez lepszą organizację i ergonomię.
Audyt 5S można przeprowadzić w kilku krokach:
Przygotowanie listy kontrolnej: Zawierającej wszystkie aspekty 5S.
Wyznaczenie zespołu audytowego: Składającego się z osób z doświadczeniem w 5S.
Przeprowadzenie audytu: Ocena każdego punktu na liście kontrolnej.
Dokumentowanie wyników: Spisanie i graficzne przedstawienie wyników.
Prezentacja wyników: Przedstawienie wyników zespołowi i kierownictwu oraz omówienie działań naprawczych.
Aby utrzymać praktyki 5S:
Regularnie sprzątaj i utrzymuj czystość.
Uporządkuj narzędzia i materiały w łatwo dostępny sposób.
Stosuj oznaczenia wizualne, takie jak etykiety i taśmy.
Przeprowadzaj rutynowe kontrole i audyty 5S.
Promuj samodyscyplinę i ciągłe doskonalenie wśród pracowników.
Minimalizacji zbędnych przedmiotów i materiałów.
Stosowaniu ergonomicznych rozwiązań, dostosowanych do potrzeb pracowników.
Wprowadzeniu systemów przechowywania, które ułatwiają porządek.
Stosowaniu oznaczeń wizualnych i instrukcji, które pomagają w utrzymaniu porządku i efektywności.
Zobacz także:
- 1.Szkolenia
- 2.Diagram Ishikawy: Narzędzie po analizie przyczynowo-skutkowej
- 3.Raport 8D: Metoda na rozwiązywanie problemów
- 4.Metody doskonalenia Systemów Zarządzania
- 5.Bezpieczeństwie informacji: Od definicji do praktycznych zastosowań
- 6.Kaizen
- 7.Audyt luk procesowych w obszarach produkcyjno-biznesowych
- 8.Mapowanie ryzyka: Identyfikacja, ocena i zarządzanie ryzykiem
- 9.Pełnomocnik oraz Audytor Wewnętrzny AS 9100
- 10.Kaizen Lean: Ciągłe doskonalenie w praktyce biznesowej
- 11.ISO 9001: od zrozumienia do certyfikacji
- 12.Metoda 5S: Zasady, wdrożenia i korzyści
- 13.Szkolenia ISO 45001: od podstaw do certyfikacji
- 14.Wdrożenie ISO: Od planowania do certyfikacji
- 15.Pełnomocnik ds. systemu zarządzania jakością: zakres obowiązków i kluczowe aspekty funkcji
- 16.Podstawowe narzędzia Lean Manufacturing
- 17.Pełnomocnik oraz Audytor Wewnętrzny AS 9100
- 18.Business Process Management: Czyli zarządzanie procesami biznesowymi
- 19.Rozwiązanie problemów: Przewodnik po skutecznych metodach i strategiach
- 20.Systemy Zarządzania
- 21.Zarządzanie procesami
- 22.Mapowanie procesu produkcji
- 23.Mapa procesu: Przewodnik po mapowaniu procesów biznesowych
- 24.Jak zostać inżynierem: Kompleksowy przewodnik krok po kroku
- 25.Diagram przepływów: Kompleksowy przewodnik po tworzeniu i zrozumieniu
- 26.Wszechstronne spojrzenie na normę IATF 16949: od historii do procesu certyfikacji
- 27.Certyfikat ISO: Korzyści i proces wdrożenia
- 28.Pełnomocnik oraz Audytor wewnętrzny ISO 9001:2015
- 29.Outsourcing Pełnomocnika ds. Systemów Zarządzania
- 30.Projektowanie i modelowanie procesów
- 31.Macierz ryzyka: Narzędzie do efektywnego zarządzania
- 32.Leadership Czyli Przywództwo: Definicje, cechy i style efektywnego lidera
- 33.Wskaźniki KPI: Klucz do efektywności i osiągania celów firmy
- 34.Zarządzanie procesowe
- 35.Wymagania normy EN 1090 / Zakładowa Kontrola Produkcji