Jak zrobić raport 8D: Kompleksowy Przewodnik po Metodyce Rozwiązywania Problemów
Umiejętność błyskawicznego i skutecznego rozwiązywania problemów to kluczowy element utrzymania przewagi konkurencyjnej. To także sposób na zapewnienie wysokiej jakości produktów i usług. Jednym z narzędzi, które zdobyło uznanie w tej dziedzinie, jest raport 8D. Ta metodyka, znana również jako Eight Disciplines Problem Solving, oferuje systematyczne podejście do identyfikacji, analizy oraz eliminacji problemów, które mogą negatywnie wpływać na funkcjonowanie przedsiębiorstwa.
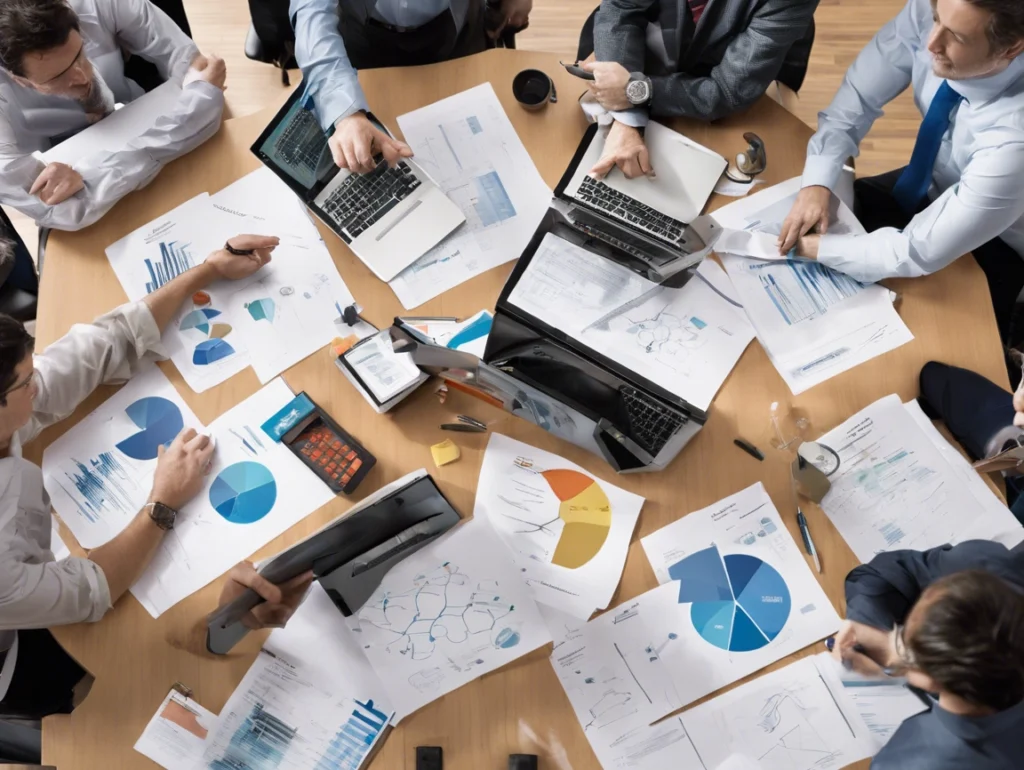
Raport 8D to jednak nie tylko narzędzie do rozwiązywania problemów. To także efektywna metoda ciągłego doskonalenia procesów. Dzięki swojej wszechstronności znajduje zastosowanie w wielu branżach – od przemysłu motoryzacyjnego po zarządzanie jakością w sektorze usług. W tym przewodniku pokażemy, jak raport 8D może pomóc w:
- identyfikacji przyczyn źródłowych problemów,
- wdrażaniu skutecznych działań korygujących,
- zapobieganiu ponownemu wystąpieniu problemów.
Odkryj, jak raport 8D może stać się kluczowym elementem strategii zarządzania jakością w Twojej firmie. To narzędzie, które prowadzi do bardziej efektywnych i trwałych rozwiązań problemów.
Spis treści
Czym jest raport 8D?
Raport 8D, czyli Eight Disciplines Problem Solving, to systematyczna metoda rozwiązywania problemów, oparta na ośmiu krokach. Jest to narzędzie zarządzania jakością, które początkowo zdobyło popularność w przemyśle motoryzacyjnym, ale jego uniwersalność sprawia, że świetnie sprawdza się także w innych branżach. Dzięki raportowi 8D organizacje mogą skutecznie identyfikować i eliminować przyczyny problemów, awarii oraz niezgodności, co prowadzi do ciągłego doskonalenia procesów.
Metodyka ta jest jednym z kluczowych narzędzi w analizie przyczyn źródłowych (RCA – root cause analysis). Oferuje standardowe, uporządkowane podejście do rozwiązywania problemów jakościowych. W przemyśle produkcyjnym, gdzie jakość produktów ma ogromne znaczenie, raport 8D staje się nieocenionym wsparciem w zarządzaniu jakością. Co więcej, jego struktura nie tylko pomaga rozwiązywać bieżące problemy, ale także wspiera proces ciągłego doskonalenia, co jest kluczowe, by utrzymać konkurencyjność na rynku.
Geneza i rozwój metody 8D
Metoda 8D, czyli Eight Disciplines Problem Solving, powstała z potrzeby stworzenia uporządkowanego podejścia do rozwiązywania problemów, które mogą negatywnie wpływać na jakość produktów i procesów. Choć dziś jest powszechnie stosowana w wielu branżach, jej początki sięgają czasów, gdy firmy zaczęły dostrzegać konieczność lepszego zarządzania jakością. Właśnie wtedy pojawiła się potrzeba bardziej systematycznego podejścia do problemów, co doprowadziło do rozwoju tej metody.
Rola Ford Motor Company w popularyzacji raportu 8D
Ford Motor Company odegrała kluczową rolę w popularyzacji metody 8D, szczególnie w przemyśle motoryzacyjnym. Firma, znana z innowacyjnych rozwiązań w produkcji i zarządzaniu jakością, wprowadziła 8D jako standardowy proces rozwiązywania problemów. Dzięki temu metoda stała się nie tylko narzędziem do tworzenia raportów 8D, ale także integralnym elementem strategii jakościowej wielu firm na całym świecie. Ford, poprzez swoje działania, przyczynił się do szerokiego uznania i adaptacji tej metody w różnych sektorach przemysłu.
Departament Obrony USA i norma MIL-STD 1520
Interesującym aspektem historii metody 8D jest jej związek z Departamentem Obrony USA. To właśnie ta instytucja opracowała metodę 8D w ramach normy MIL-STD 1520, która miała na celu zarządzanie niezgodnościami materiałowymi. Norma ta stanowiła fundament dla metody 8D, oferując ramy dla systematycznego podejścia do rozwiązywania problemów. Dzięki temu 8D zyskało solidne podstawy teoretyczne i praktyczne, co umożliwiło jej dalszy rozwój i szeroką adaptację w różnych branżach.
8 kroków raportu 8D
Raport 8D to metoda składająca się z ośmiu kluczowych kroków, które mają na celu skuteczne rozwiązywanie problemów. Każdy z tych etapów odgrywa istotną rolę w procesie identyfikacji, analizy i eliminacji problemów, które mogą wpływać na funkcjonowanie organizacji. Poniżej znajdziesz przegląd tych kroków:
Krok D1: Utworzenie grupy roboczej
Pierwszym krokiem w raporcie 8D jest utworzenie grupy roboczej. To interdyscyplinarny zespół, który powinien składać się z przedstawicieli różnych działów firmy. Ważne, aby grupa miała zróżnicowane kompetencje, co pozwala spojrzeć na problem z różnych perspektyw. Zespół musi mieć wyznaczonego lidera oraz odpowiednie uprawnienia, co umożliwia skuteczne działanie i realizację raportu 8D.
Krok D2: Dokładny opis problemu (metoda 5W2H)
Precyzyjny opis problemu to klucz do zrozumienia jego natury i skali. W tym celu stosuje się metodę 5W2H, która pomaga zebrać szczegółowe informacje. Opis powinien obejmować:
- miejsce wystąpienia problemu,
- czas, w którym problem się pojawił,
- liczbę wadliwych sztuk,
- sposób identyfikacji problemu,
- potencjalne zagrożenia dla klienta.
Dzięki temu można dokładnie określić, z czym mamy do czynienia i jakie działania należy podjąć.
Krok D3: Tymczasowe działania korygujące
Po zidentyfikowaniu problemu należy podjąć tymczasowe działania korygujące. To natychmiastowe kroki, które mają na celu:
- zminimalizowanie skutków problemu,
- przywrócenie ciągłości produkcji,
- ograniczenie ryzyka dla firmy i klienta.
Tymczasowe działania są kluczowe, zanim zostaną wdrożone trwałe rozwiązania.
Krok D4: Identyfikacja przyczyny źródłowej (metody 5WHY i Diagram Ishikawy)
Identyfikacja przyczyny źródłowej problemu to jeden z najważniejszych etapów raportu 8D. W tym celu stosuje się narzędzia takie jak Diagram Ishikawy oraz metoda 5WHY. Diagram Ishikawy, znany również jako diagram przyczyn i skutków, pomaga w analizie przyczyn problemów, natomiast metoda 5WHY polega na zadawaniu serii pytań „dlaczego”, aby dotrzeć do źródła problemu. Dzięki tym narzędziom można dokładnie zrozumieć, co leży u podstaw problemu.
Krok D5: Stałe działania korygujące
Po zidentyfikowaniu przyczyny źródłowej, kolejnym krokiem jest wdrożenie stałych działań korygujących. Mają one na celu:
- wyeliminowanie przyczyn problemu,
- zapobieżenie jego powtórzeniu,
- wprowadzenie dodatkowej kontroli,
- naprawę wadliwych wyrobów,
- poinformowanie dostawcy o defektach.
Stałe działania korygujące są kluczowe, aby upewnić się, że problem nie pojawi się ponownie.
Krok D6: Weryfikacja skuteczności działań korygujących
Weryfikacja skuteczności działań korygujących polega na sprawdzeniu, czy wprowadzone działania były skuteczne i czy przyczyna źródłowa została prawidłowo określona. To etap, który pozwala ocenić, czy podjęte kroki przyniosły oczekiwane rezultaty i czy problem został trwale rozwiązany.
Krok D7: Akcje zapobiegawcze
Akcje zapobiegawcze to działania podejmowane w celu zapobieżenia ponownemu wystąpieniu problemu. Mogą obejmować:
- modyfikację procesu,
- zmianę narzędzi,
- zmianę procedur,
- aktualizację dokumentacji.
Dzięki akcjom zapobiegawczym firma może uniknąć podobnych problemów w przyszłości, co przyczynia się do ciągłego doskonalenia procesów.
Krok D8: Uznanie dla zespołu i zamknięcie raportu
Ostatnim krokiem w procesie raportu 8D jest ocena i zamknięcie raportu. Powinno to obejmować:
- podsumowanie skuteczności wdrożonych działań,
- archiwizację raportu jako bazy wiedzy na przyszłość,
- docenienie zespołu, który przyczynił się do rozwiązania problemu.
Docenienie zespołu motywuje do dalszej pracy i zaangażowania w procesy doskonalenia.
Narzędzia wspierające analizę w raporcie 8D
W procesie tworzenia raportu 8D, narzędzia analityczne odgrywają fundamentalną rolę. Nie tylko pomagają one zidentyfikować źródła problemów, ale również wspierają w opracowywaniu skutecznych działań naprawczych. Do najczęściej stosowanych narzędzi należą:
- Analiza Pareto
- Diagram Ishikawy
- FMEA
- SPC
- Metoda 5WHY
Każde z tych narzędzi pełni specyficzną funkcję w procesie rozwiązywania problemów, dostarczając zespołom niezbędnych informacji do podejmowania świadomych i trafnych decyzji.
Diagram Ishikawy
Diagram Ishikawy, znany również jako diagram przyczyn i skutków, to jedno z kluczowych narzędzi wykorzystywanych w analizie problemów w raporcie 8D. Jego głównym celem jest wizualizacja wszystkich możliwych przyczyn problemu, co pozwala zespołowi lepiej zrozumieć, jakie czynniki mogą wpływać na daną sytuację. Diagram przypomina kształtem rybi szkielet – głowa symbolizuje problem, a ości reprezentują różne kategorie przyczyn. Dzięki temu narzędziu zespoły mogą skutecznie analizować i identyfikować kluczowe obszary wymagające interwencji.
Metoda 5WHY
Metoda 5WHY to prosta, ale niezwykle skuteczna technika zadawania pytań „dlaczego”, stosowana w raporcie 8D do odkrywania pierwotnych przyczyn problemów. Proces polega na zadawaniu serii pytań, które prowadzą do zidentyfikowania głównej przyczyny problemu. Zadając pytanie „dlaczego” pięć razy, zespoły mogą dotrzeć do sedna problemu, co jest kluczowe dla opracowania trwałych rozwiązań. Ta metoda sprawdza się szczególnie dobrze w sytuacjach, gdzie problem wydaje się złożony lub trudny do zrozumienia na pierwszy rzut oka.
Analiza Pareto
Analiza Pareto to narzędzie, które pomaga zidentyfikować najczęstsze przyczyny problemów w raporcie 8D. Opiera się na zasadzie Pareto, która mówi, że 80% problemów wynika z 20% przyczyn. Dzięki tej analizie zespoły mogą skupić swoje wysiłki na kluczowych przyczynach, które mają największy wpływ na problem. Wykorzystanie analizy Pareto pozwala na efektywne rozwiązywanie problemów, koncentrując się na najważniejszych aspektach wymagających poprawy.
FMEA (Failure Mode and Effects Analysis)
FMEA, czyli Failure Mode and Effects Analysis, to narzędzie stosowane w raporcie 8D do identyfikacji i oceny ryzyka awarii w procesie. Analiza ta pozwala zrozumieć, jakie potencjalne awarie mogą wystąpić, jakie będą ich skutki oraz jak można im zapobiec. Dzięki FMEA zespoły mogą proaktywnie zarządzać ryzykiem, co jest kluczowe dla zapewnienia ciągłości i jakości procesów. Wiedza o tym, jak skutecznie wykorzystać FMEA w raporcie 8D, jest nieoceniona dla każdej organizacji, która dąży do doskonałości operacyjnej.
SPC (Statistical Process Control)
SPC, czyli Statistical Process Control, to narzędzie stosowane w raporcie 8D do monitorowania stabilności procesów produkcyjnych. Dzięki zastosowaniu statystycznych metod kontroli, SPC pozwala na identyfikację odchyleń od normy, co umożliwia szybkie reagowanie na potencjalne problemy. Analizując przyczyny problemów za pomocą SPC, organizacje mogą zapewnić, że ich procesy pozostają w granicach kontrolnych, co jest kluczowe dla utrzymania wysokiej jakości produktów i usług.
Akcje korygujące i zapobiegawcze w raporcie 8D
Raport 8D to narzędzie, które odgrywa kluczową rolę w rozwiązywaniu problemów, oferując uporządkowane podejście do ich identyfikacji i eliminacji. Jednym z najważniejszych elementów tego raportu są działania korygujące oraz zapobiegawcze. Te kroki nie tylko pomagają przywrócić normalne funkcjonowanie procesów, ale także zapobiegają przyszłym problemom. Przyjrzyjmy się bliżej, jak te działania są wdrażane w ramach raportu 8D, aby lepiej zrozumieć ich znaczenie.
Tymczasowe działania korygujące
Tymczasowe działania korygujące to natychmiastowe kroki podejmowane, by zminimalizować skutki problemu i przywrócić ciągłość produkcji. Wyobraź sobie sytuację, w której linia produkcyjna nagle przestaje działać z powodu niespodziewanego defektu. Takie działania działają jak szybka interwencja, pozwalając na kontynuację produkcji, zanim zostaną wdrożone bardziej trwałe rozwiązania. Dzięki nim można:
- ograniczyć przestoje,
- utrzymać zadowolenie klienta,
- zapewnić ciągłość produkcji,
- zminimalizować skutki problemu.
W dynamicznym środowisku produkcyjnym, szybka reakcja jest kluczowa dla utrzymania płynności operacji.
Stałe działania korygujące
Po zidentyfikowaniu przyczyny źródłowej problemu, kolejnym krokiem jest wdrożenie stałych działań korygujących. Ich celem jest całkowite wyeliminowanie przyczyn problemu, aby zapobiec jego powtórzeniu. W praktyce może to oznaczać:
- wprowadzenie nowych procedur,
- modyfikację istniejących procesów,
- zmianę dostawcy komponentów,
- aktualizację narzędzi lub technologii.
Skuteczne działania korygujące są kluczowe, by problem nie pojawił się ponownie, co ma bezpośredni wpływ na długoterminowy sukces organizacji.
Akcje zapobiegawcze
Ostatnim, ale równie istotnym elementem są akcje zapobiegawcze. Te działania mają na celu zapobieżenie ponownemu wystąpieniu problemu w przyszłości. Mogą obejmować:
- modyfikację procesów,
- zmianę narzędzi,
- aktualizację procedur,
- udoskonalenie dokumentacji.
Dzięki nim organizacja może skutecznie unikać podobnych problemów w przyszłości, co przyczynia się do ciągłego doskonalenia procesów. W ten sposób raport 8D nie tylko rozwiązuje bieżące problemy, ale także tworzy solidne fundamenty dla bardziej stabilnej i efektywnej przyszłości.
Zastosowanie raportu 8D w różnych branżach
Raport 8D to narzędzie o szerokim zastosowaniu, które znajduje swoje miejsce w wielu sektorach. Jego uporządkowane podejście do identyfikacji i eliminacji problemów czyni go niezwykle efektywnym w różnych środowiskach biznesowych. Przyjrzyjmy się, jak raport 8D funkcjonuje w przemyśle motoryzacyjnym oraz w zarządzaniu jakością w innych branżach.
Przemysł motoryzacyjny
W branży motoryzacyjnej, gdzie jakość i bezpieczeństwo są absolutnymi priorytetami, raport 8D odgrywa kluczową rolę. Standard VDA 4, czyli niemiecki standard jakości, stanowi fundament dla pytań kontrolnych stosowanych w procesie 8D. Dzięki temu firmy motoryzacyjne mogą systematycznie analizować i rozwiązywać problemy jakościowe, co jest niezbędne do utrzymania najwyższych standardów produkcji.
Przykłady zastosowania raportu 8D w przemyśle motoryzacyjnym:
- Szybka identyfikacja przyczyny defektu w produkcji.
- Minimalizacja ryzyka powtórzenia się problemu.
- Zachowanie ciągłości produkcji na najwyższym poziomie.
Zarządzanie jakością w innych sektorach
Raport 8D znajduje również szerokie zastosowanie w zarządzaniu jakością w innych branżach. Gdy klienci zgłaszają reklamacje dotyczące jakości produktów, raport 8D umożliwia dogłębną analizę i identyfikację źródła problemu. Podobnie, niezgodności wewnętrzne, czyli problemy jakościowe występujące wewnątrz organizacji, oraz niezgodności zewnętrzne, zgłaszane przez klientów, są skutecznie rozwiązywane za pomocą tej metody.
Korzyści z zastosowania raportu 8D w zarządzaniu jakością:
- Poprawa jakości produktów i usług.
- Budowanie zaufania klientów.
- Skuteczne rozwiązywanie reklamacji i niezgodności.
- Wzrost długoterminowego sukcesu organizacji.
Powiązania raportu 8D z innymi metodami zarządzania jakością
Raport 8D to niezwykle skuteczna metoda rozwiązywania problemów, ale nie funkcjonuje w izolacji. Często jest łączony z innymi narzędziami zarządzania jakością, co pozwala na osiągnięcie jeszcze lepszych wyników. W tej części przyjrzymy się, jak raport 8D współpracuje z innymi podejściami, tworząc spójny i efektywny system zarządzania jakością.
Cykl PDCA (Plan-Do-Check-Act)
Jednym z kluczowych fundamentów, na których opiera się metodologia 8D, jest cykl PDCA (Plan-Do-Check-Act), znany również jako cykl Deminga. PDCA to iteracyjny proces, który umożliwia organizacjom:
- planowanie działań,
- wdrażanie zaplanowanych działań,
- monitorowanie wyników,
- wprowadzanie niezbędnych poprawek.
Dzięki temu raport 8D nie tylko rozwiązuje bieżące problemy, ale także wspiera ciągłe doskonalenie procesów. A to właśnie ciągłe doskonalenie jest fundamentem skutecznego zarządzania jakością.
Jidoka w Lean Management
Innym podejściem, które często współpracuje z raportem 8D, jest Jidoka – kluczowy element Lean Management. Jidoka to metoda automatyzacji z wbudowaną kontrolą jakości, która pozwala natychmiast zatrzymać proces produkcyjny, gdy tylko wykryty zostanie problem. W połączeniu z raportem 8D, Jidoka umożliwia:
- szybkie wykrywanie problemów,
- natychmiastowe zatrzymanie procesu,
- zapobieganie powtórzeniu problemu,
- utrzymanie wysokiej jakości produktów i procesów.
Dzięki tej synergii organizacje mogą skutecznie identyfikować i eliminować przyczyny problemów, zanim wpłyną one na końcowy produkt.
Standard VDA 4
W branży motoryzacyjnej raport 8D często opiera się na niemieckim standardzie VDA 4. Ten standard dostarcza szczegółowych list kontrolnych, które są wykorzystywane w raporcie 8D, aby zapewnić zgodność z wymaganiami jakościowymi. Infografika raportu 8D, oparta na VDA 4, wspiera:
- systematyczne podejście do analizy,
- skuteczne rozwiązywanie problemów,
- utrzymanie wysokich standardów jakości w przemyśle motoryzacyjnym.
Przykłady i szablony raportu 8D
Wdrażanie raportu 8D w firmie? To może być znacznie prostsze, jeśli masz pod ręką gotowy szablon. Szablon raportu 8D to narzędzie, które prowadzi Cię krok po kroku przez każdy z ośmiu etapów. Dzięki temu nie musisz się martwić, że coś istotnego zostanie pominięte. Zamiast tracić czas na tworzenie dokumentu od podstaw, zespół może skupić się na tym, co naprawdę ważne – analizie problemu i znalezieniu skutecznych rozwiązań. Proste, prawda?
Przykład wypełnionego raportu 8D
Chcesz zobaczyć, jak to wygląda w praktyce? Warto zerknąć na przykład raportu 8D, który został wypełniony zgodnie z tą metodą. Taki dokument zawiera:
- szczegółowy opis problemu,
- tymczasowe działania korygujące,
- trwałe działania korygujące,
- wnioski z analizy przyczyn źródłowych.
To doskonałe źródło wiedzy zarówno dla tych, którzy dopiero zaczynają swoją przygodę z 8D, jak i dla bardziej doświadczonych zespołów, które chcą doskonalić swoje umiejętności w rozwiązywaniu problemów. Warto się zainspirować!
Pobierz szablon raportu 8D
Jeśli chcesz rozpocząć pracę z raportem 8D, masz do wyboru różne formularze raportu 8D do pobrania. Najczęściej są one dostępne w formatach edytowalnych, co pozwala na ich łatwe dostosowanie do specyficznych potrzeb Twojej organizacji. Pobranie szablonu to pierwszy krok do wdrożenia tej metodyki w firmie. To narzędzie, które pomoże Ci skutecznie zarządzać jakością i rozwiązywać problemy. Gotowy na zmiany?
Zalety i wyzwania związane z wdrażaniem raportu 8D
Wdrażanie raportu 8D w firmie to doskonały sposób na poprawę jakości, ale – jak to często bywa – nie jest to proces bez wyzwań. Ta metoda działa, ponieważ umożliwia systematyczne rozwiązywanie problemów, co jest kluczowe, jeśli chcemy utrzymać wysoką jakość produktów i procesów. Jednak, aby wszystko przebiegło zgodnie z planem, niezbędne jest odpowiednie podejście oraz pełne zaangażowanie zespołu. Bez tego, nawet najlepsza metoda może nie przynieść oczekiwanych rezultatów. A przecież nikt nie chce, by wysiłki poszły na marne.
Główne zalety raportu 8D
Jedną z największych zalet raportu 8D jest jego przejrzystość i logiczna struktura. Krok po kroku prowadzi zespół przez cały proces rozwiązywania problemów, co znacząco ułatwia skuteczne działanie. Dlatego właśnie raport 8D cieszy się tak dużą popularnością, zwłaszcza w branży motoryzacyjnej, gdzie stanowi standard do dokumentowania reklamacji i działań naprawczych. Dzięki temu strukturalnemu podejściu można dokładnie przeanalizować problem, co jest nieocenione w zarządzaniu jakością i zapobieganiu powtarzaniu się tych samych błędów. To narzędzie, które pozwala nie tylko rozwiązać problem, ale i zapobiec jego powrotowi.
Najczęściej popełniane błędy przy wdrażaniu raportu 8D
Mimo licznych zalet, wdrażanie raportu 8D nie zawsze przebiega bezproblemowo. Najczęstsze błędy to:
- powierzchowna analiza przyczyn,
- brak pełnego zaangażowania zespołu,
- niewłaściwe działania korygujące,
- brak systematycznego monitorowania postępów.
Każdy z tych błędów może poważnie osłabić skuteczność działań naprawczych, co w efekcie może prowadzić do niepełnego rozwiązania problemu. Dlatego tak istotne jest, aby zespół był dobrze przeszkolony i w pełni zaangażowany w cały proces. Tylko wtedy można w pełni wykorzystać potencjał raportu 8D. A przecież o to właśnie chodzi – o skuteczność i trwałe rozwiązania.
Podsumowanie: Skuteczność raportu 8D w rozwiązywaniu problemów
Raport 8D to narzędzie, które zyskało szerokie uznanie w wielu branżach – od motoryzacji po sektor usługowy. Jego systematyczne podejście umożliwia dogłębną analizę problemów, precyzyjne określenie przyczyn źródłowych oraz wdrożenie skutecznych działań korygujących i zapobiegawczych. W efekcie firmy nie tylko rozwiązują bieżące trudności, ale także zapobiegają ich ponownemu wystąpieniu. A to, jak wiadomo, jest kluczowe dla utrzymania wysokiej jakości produktów i procesów.
Jednym z najważniejszych czynników wpływających na efektywność raportu 8D jest jego zdolność do angażowania zespołów w proces rozwiązywania problemów. Interdyscyplinarne grupy robocze, które stanowią fundament metodyki 8D, pozwalają spojrzeć na problem z różnych perspektyw, co prowadzi do znalezienia optymalnych rozwiązań. Takie podejście nie tylko zwiększa szanse na skuteczne rozwiązanie, ale także wspiera rozwój kultury ciągłego doskonalenia w organizacji.
Warto również pamiętać, że raport 8D nie funkcjonuje w oderwaniu od innych narzędzi. Jego integracja z metodami zarządzania jakością, takimi jak:
- cykl PDCA (Plan-Do-Check-Act)
- Jidoka (automatyzacja z ludzkim nadzorem)
tworzy spójny system, który jest w stanie sprostać nawet najbardziej złożonym wyzwaniom. Dzięki temu organizacje mogą nie tylko reagować na problemy, ale także proaktywnie zarządzać jakością, co jest kluczowe dla długoterminowego sukcesu.
Podsumowując, raport 8D to nie tylko narzędzie do rozwiązywania problemów, ale także strategia zarządzania jakością, która pomaga firmom dążyć do doskonałości operacyjnej. Jego skuteczność w identyfikacji i eliminacji problemów sprawia, że jest nieocenionym wsparciem dla każdej organizacji, która pragnie utrzymać wysokie standardy jakości i zadowolenie klientów.
FAQ
Raport 8D to metoda rozwiązywania problemów składająca się z ośmiu kroków, znana jako Eight Disciplines Problem Solving. Stosowana jest głównie w zarządzaniu jakością do identyfikacji, analizy i eliminacji problemów w procesach produkcyjnych i operacyjnych.
Identyfikacja przyczyn źródłowych problemów.
Wdrożenie działań korygujących.
Zapobieganie ponownemu wystąpieniu problemów.
Ciągłe doskonalenie procesów.
Utworzenie grupy roboczej.
Dokładny opis problemu (np. za pomocą metody 5W2H).
Tymczasowe działania korygujące.
Identyfikacja przyczyny źródłowej (metody 5WHY, Diagram Ishikawy).
Stałe działania korygujące.
Weryfikacja skuteczności działań.
Akcje zapobiegawcze.
Uznanie dla zespołu i zamknięcie raportu.
Chociaż raport 8D powstał w przemyśle motoryzacyjnym, jego zastosowanie jest szerokie. Stosowany jest w produkcji, zarządzaniu jakością, przemyśle usługowym oraz w innych branżach, gdzie wymagane jest systematyczne rozwiązywanie problemów.
Metoda 5WHY.
Diagram Ishikawy.
Analiza Pareto.
FMEA (Failure Mode and Effects Analysis).
SPC (Statistical Process Control).
To działania podejmowane natychmiast po identyfikacji problemu, mające na celu zminimalizowanie jego skutków i zapewnienie ciągłości produkcji do czasu wdrożenia trwałych rozwiązań.
Diagram Ishikawy, nazywany również diagramem przyczyn i skutków, jest narzędziem do analizy problemów, które pomaga zidentyfikować różne przyczyny wpływające na dany problem.
Metoda 5WHY polega na zadawaniu pytania „dlaczego” pięć razy (lub więcej), aby dotrzeć do źródłowej przyczyny problemu. Pomaga to odkryć pierwotne przyczyny problemów, które mogą nie być oczywiste na początku.
Powierzchowna analiza problemu.
Brak pełnego zaangażowania zespołu.
Nieprawidłowe działania korygujące.
Brak weryfikacji skuteczności działań.
Poprawa jakości produktów i procesów.
Zmniejszenie ryzyka powtórzenia się problemów.
Skuteczniejsze zarządzanie reklamacjami i niezgodnościami.
Zwiększenie zaangażowania zespołu w proces doskonalenia.
Zobacz także:
- 1.Szkolenia
- 2.Diagram Ishikawy: Narzędzie po analizie przyczynowo-skutkowej
- 3.Raport 8D: Metoda na rozwiązywanie problemów
- 4.Metody doskonalenia Systemów Zarządzania
- 5.Bezpieczeństwie informacji: Od definicji do praktycznych zastosowań
- 6.Kaizen
- 7.Audyt luk procesowych w obszarach produkcyjno-biznesowych
- 8.Mapowanie ryzyka: Identyfikacja, ocena i zarządzanie ryzykiem
- 9.Pełnomocnik oraz Audytor Wewnętrzny AS 9100
- 10.Kaizen Lean: Ciągłe doskonalenie w praktyce biznesowej
- 11.ISO 9001: od zrozumienia do certyfikacji
- 12.Metoda 5S: Zasady, wdrożenia i korzyści
- 13.Szkolenia ISO 45001: od podstaw do certyfikacji
- 14.Wdrożenie ISO: Od planowania do certyfikacji
- 15.Pełnomocnik ds. systemu zarządzania jakością: zakres obowiązków i kluczowe aspekty funkcji
- 16.Podstawowe narzędzia Lean Manufacturing
- 17.Pełnomocnik oraz Audytor Wewnętrzny AS 9100
- 18.Business Process Management: Czyli zarządzanie procesami biznesowymi
- 19.Rozwiązanie problemów: Przewodnik po skutecznych metodach i strategiach
- 20.Systemy Zarządzania
- 21.Zarządzanie procesami
- 22.Mapowanie procesu produkcji
- 23.Mapa procesu: Przewodnik po mapowaniu procesów biznesowych
- 24.Jak zostać inżynierem: Kompleksowy przewodnik krok po kroku
- 25.Diagram przepływów: Kompleksowy przewodnik po tworzeniu i zrozumieniu
- 26.Wszechstronne spojrzenie na normę IATF 16949: od historii do procesu certyfikacji
- 27.Certyfikat ISO: Korzyści i proces wdrożenia
- 28.Pełnomocnik oraz Audytor wewnętrzny ISO 9001:2015
- 29.Outsourcing Pełnomocnika ds. Systemów Zarządzania
- 30.Projektowanie i modelowanie procesów
- 31.Macierz ryzyka: Narzędzie do efektywnego zarządzania
- 32.Leadership Czyli Przywództwo: Definicje, cechy i style efektywnego lidera
- 33.Wskaźniki KPI: Klucz do efektywności i osiągania celów firmy
- 34.Zarządzanie procesowe
- 35.Wymagania normy EN 1090 / Zakładowa Kontrola Produkcji
- 36.Cykl PDCA (Plan-Do-Check-Act): Klucz do ciągłego doskonalenia w praktyce
- 37.Rozwiązywanie problemów w Systemach Zarządzania
- 38.Polityka Jakości: od teorii do praktyki
- 39.Kompleksowy przewodnik po bezpieczeństwie informacji: kluczowe elementy w ochronie firm
- 40.ISO 31000: Klucz do skutecznego zarządzania ryzykiem
- 41.Mocne strony: Jak je zidentyfikować, rozwijać i skutecznie prezentować
- 42.Kultura organizacyjna: Definicja, znaczenie i wpływ na rozwój firmy
- 43.Model SMART: Kompleksowy przewodnik po skutecznym wyznaczaniu celów
- 44.Lean thinking: Podejście do optymalizacji procesów
- 45.Wdrażanie Lean Manufacturing w Przedsiębiorstwach Produkcyjnych
- 46.Standaryzacja: Klucz do optymalizacji i doskonalenia procesów w przedsiębiorstwie
- 47.Jak obliczyć produktywność: Czyli do pomiaru i zwiększania wydajności pracy
- 48.Metoda SMART: Kompleksowy przewodnik po skutecznym wyznaczaniu celów
- 49.ISO 13485:2016 – System Zarządzania Jakością w wyrobach medycznych
- 50.Pełnomocnik oraz Audytor Wewnętrzny ISO 13485:2016
- 51.Wyrób niezgodny – Pełny poradnik dotyczący rozpoznawania, zarządzania i podejmowania działań
- 52.FDA: Kompleksowy przewodnik po amerykańskiej Agencji ds. Żywności i Leków
- 53.Certyfikat jakości żywności: Klucz do gwarancji bezpieczeństwa i jakości produktów spożywczych
- 54.Przygotowanie do Audytu ISO: Twój Przewodnik Krok po Kroku
- 55.Wymagania ISO 22000:2018 – System Zarządzania Bezpieczeństwem Żywności
- 56. Czym jest analiza SWOT – klucz do odkrycia potencjału Twojego biznesu
- 57.Audyt Trzeciej Strony: Twoja Droga do Certyfikacji ISO
- 58.Kompleksowy przewodnik po szkoleniu TISAX: Wymagania, procesy i korzyści
- 59.Certyfikacja TISAX: Kompleksowy przewodnik po wymaganiach, procesach i korzyściach
- 60.VDA 6.3 – Audyt procesów zgodnych z normą niemieckiego przemysłu motoryzacyjnego
- 61.TISAX compliance czyli zrozumienie zgodności TISAX
- 62.TISAX – System Zarządzania Bezpieczeństwem Informacji w branży motoryzacyjnej
- 63.Metody zarządzania produkcją w przemyśle XXI wieku
- 64.Manufacturing – Wszechstronne spojrzenie na przemysł produkcyjny: procesy, techniki i strategie
- 65.Narzędzia zarządzania jakością: od klasycznych metod do nowoczesnych rozwiązań
- 66.Audyt Systemu Zarządzania Jakością: od przygotowania do wyników
- 67.ISO 9001:2015 – System Zarządzania Jakością
- 68.Mapowanie strumienia wartości: Kompleksowy przewodnik po procesie i jego znaczeniu
- 69.Zasady Lean Management: Eliminacja marnotrawca i poprawa jakości